Welding quality assessment is an essential part of ensuring the safety, reliability, and durability of welded structures in various industries, including manufacturing, construction, and transportation. Within this relevant context the POWERDECK™ (POwer Industry Welding Equipment and Robots regulation using AI Data Enhancement and Certification Kits) project was awarded to MYWAI S.r.l. (www.myw.ai) by the EU KITT4SME initiative (kitt4sme.eu).
In the project MYWAY S.r.l. acted as leading partner contributing its expertise in Industry 4.0 readiness assessment and equipment servitization consultancy, industrial IoT sensors and edge devices design and implementation, besides advanced AI skills and know how in signal/image processing, pattern recognition, machine learning methods. Other engaged partners were SDG Studio (www.sdgstudio.it), a specialized Industry 4.0 system integrator expert in open standards and protocols, to address the quality improvement needs of San Giorgio SEIGEN S.p.A. (www.sg-seigen.com), a welding services provider for the manufacturing of large power vessels, casings and components used by leading power industry general contractors such as Ansaldo Energia, Siemens Energy and General Electric.
The POWERDECK™ Action was primarily focused on the assessment of welding processes outcomes through the AI-based real time detection of anomalies in the key welding parameters. To this end, the project aimed at extending the technological framework developed by the KITT4SME initiative by integrating new AI models designed, developed, trained, and tested using the preexisting functionalities made available by the MYWAI Equipment as a Service (EaaS) platform. This integration is expected to enable the POWERDECK™ solution providing real-time insights “at the edge” of welding process, thus helping the early identification of potential issues and prevent defects in the final products.
The POWERDECK™ platform’s ability to collect and analyze real-time welding data from sensors, welders, and the environment can provide invaluable insights to San Giorgio Seigen’s welding teams. By monitoring key parameters like current, voltage, energy, wire feed speed, the AI models can detect subtle anomalies and potential defects early on. This proactive approach can prevent rework, reduce scrap rates, and ensure the production of consistently high-quality welds.
The POWERDECK™ Action has indirectly received funding from the European Union’s Horizon 2020 research and innovation programme, via an Open Call issued and executed under project KITT4SME (grant agreement № 952119).
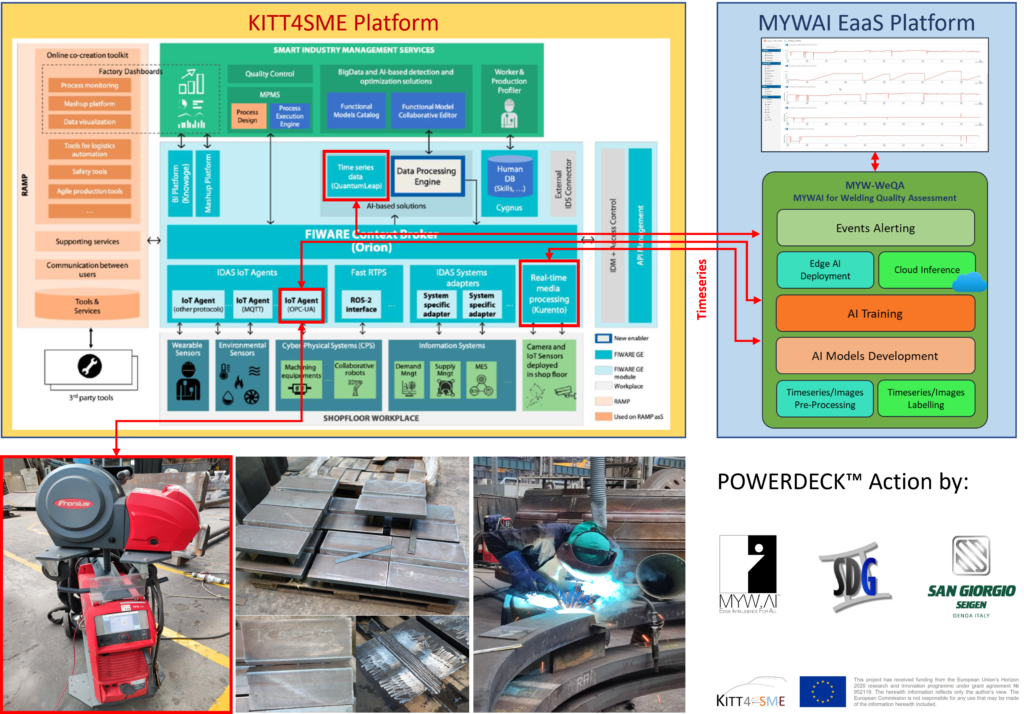